Understanding the Role of Quality Control in Mixed Cat Litter Manufacturing
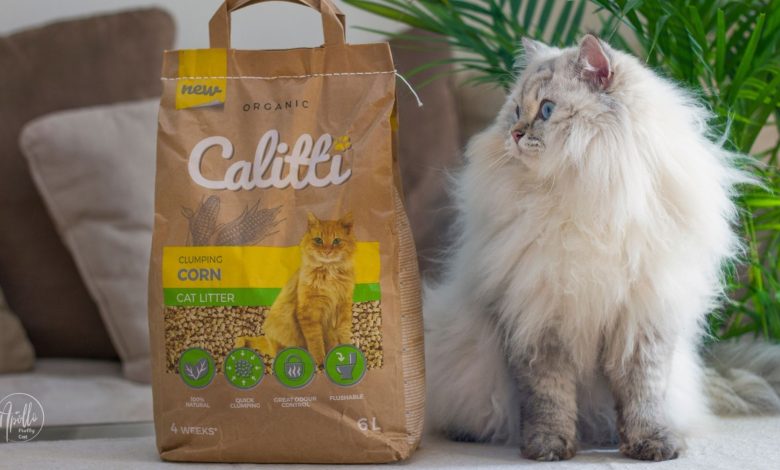
Quality control is a cornerstone of manufacturing, ensuring that products meet specific standards and perform reliably. In the cat litter industry, where functionality and safety are paramount, quality control plays a crucial role in delivering a product that satisfies consumer expectations and regulatory requirements. This blog explores the importance of quality control in Mixed cat litter manufacturer, examining the processes, challenges, and best practices involved in ensuring product excellence.
1. The Importance of Quality Control
Ensuring Product Consistency
- Uniform Performance: Quality control ensures that each batch of mixed cat litter performs consistently. This includes maintaining uniform clumping ability, absorbency, and odor control, which are critical factors for consumer satisfaction.
- Brand Reliability: Consistent quality helps build consumer trust and brand loyalty. When customers know they can rely on a product to perform well, they are more likely to repurchase and recommend it.
Meeting Regulatory Standards
- Compliance: Manufacturers must adhere to various regulatory standards, which may include safety, environmental, and performance regulations. Quality control helps ensure that products comply with these standards, avoiding legal issues and potential recalls.
- Safety Assurance: Ensuring that the product is free from harmful contaminants and allergens is crucial for consumer safety. Quality control processes are designed to identify and eliminate potential risks.
2. Quality Control Processes in Mixed Cat Litter Manufacturing
Raw Material Testing
- Material Inspection: Before production begins, raw materials are inspected and tested for quality. This includes evaluating properties such as moisture content, particle size, and chemical composition.
- Supplier Quality Assurance: Manufacturers work closely with suppliers to ensure that raw materials meet specified quality standards. This involves establishing criteria for material acceptance and conducting regular audits of supplier practices.
In-Process Quality Control
- Blending and Formulation Checks: During the blending process, quality control checks are performed to ensure that the materials are mixed according to the correct ratios and specifications. This includes monitoring the consistency of the blend and making adjustments as needed.
- Granulation and Conditioning Monitoring: The granulation and conditioning stages are closely monitored to ensure that the product achieves the desired texture and performance characteristics. Quality control involves checking for uniformity and detecting any deviations from the target specifications.
Performance Testing
- Clumping Ability: One of the key performance tests for cat litter is its clumping ability. Quality control tests evaluate how well the litter forms clumps when it comes into contact with moisture, ensuring that it performs as expected.
- Absorbency and Odor Control: Tests are conducted to assess the litter’s absorbency and odor control capabilities. These tests simulate real-world conditions to determine how effectively the litter manages moisture and neutralizes odors.
Final Product Inspection
- Visual Inspection: The finished product undergoes visual inspection to check for any defects, such as irregular granule sizes or packaging issues. This helps ensure that the product is aesthetically appealing and free from physical defects.
- Packaging Quality: Quality control extends to packaging, ensuring that it is properly sealed, labeled, and free from damage. Packaging quality checks help prevent contamination and ensure that product information is accurate and complete.
3. Challenges in Quality Control
Material Variability
- Consistency Issues: Variability in raw materials can affect the consistency of the final product. Quality control must address these challenges by implementing robust testing and blending procedures to minimize the impact of material variations.
- Supplier Dependability: Ensuring that suppliers consistently deliver high-quality materials can be challenging. Manufacturers need to maintain strong relationships with suppliers and conduct regular quality assessments to mitigate risks.
Process Optimization
- Balancing Efficiency and Quality: Achieving a balance between production efficiency and quality can be challenging. Manufacturers must optimize processes to ensure that quality is maintained without compromising production speed or increasing costs.
- Technology Integration: Incorporating new technologies into the quality control process can pose challenges. Manufacturers need to invest in advanced testing equipment and train staff to effectively use these technologies.
4. Best Practices for Effective Quality Control
Implementing a Quality Management System
- ISO Standards: Adopting international quality management standards, such as ISO 9001, helps establish a structured approach to quality control. These standards provide a framework for managing quality processes and ensuring continuous improvement.
- Documentation and Record-Keeping: Maintaining thorough documentation of quality control procedures, test results, and corrective actions is essential for tracking performance and addressing issues promptly.
Training and Development
- Staff Training: Regular training for quality control staff ensures that they are knowledgeable about the latest testing methods, equipment, and industry standards. Well-trained personnel are better equipped to identify and address quality issues.
- Continuous Improvement: Fostering a culture of continuous improvement encourages staff to seek ways to enhance quality control processes. This includes regularly reviewing procedures and implementing feedback to drive improvements.
Customer Feedback Integration
- Monitoring Feedback: Collecting and analyzing customer feedback provides valuable insights into product performance and quality. Manufacturers can use this feedback to identify areas for improvement and make necessary adjustments to the product.
- Proactive Problem-Solving: Addressing potential quality issues before they reach the market is crucial. Manufacturers should implement proactive measures to detect and resolve problems during production, reducing the likelihood of recalls or customer complaints.
5. The Future of Quality Control in Cat Litter Manufacturing
Advancements in Testing Technologies
- Automation and Smart Sensors: The integration of automation and smart sensors in quality control processes enhances precision and efficiency. These technologies provide real-time monitoring and analysis, allowing for quicker detection of deviations and more accurate testing.
- Advanced Analytical Techniques: Emerging analytical techniques, such as spectroscopy and microscopy, offer more detailed insights into the properties of cat litter materials. These advancements contribute to a deeper understanding of product performance and quality.
Sustainability Considerations
- Eco-Friendly Practices: As manufacturers focus on sustainability, quality control processes will need to adapt to accommodate eco-friendly materials and practices. This includes evaluating the performance of biodegradable materials and ensuring compliance with environmental regulations.
- Lifecycle Assessment: Quality control may increasingly involve lifecycle assessments to evaluate the environmental impact of products from production through disposal. This holistic approach helps manufacturers make more informed decisions about sustainability.
Conclusion
Quality control is essential in mixed cat litter manufacturing, ensuring that products meet performance standards, regulatory requirements, and consumer expectations. By implementing robust quality control processes, addressing challenges, and embracing best practices, manufacturers can deliver high-quality products that satisfy both pets and their owners.
As the industry evolves, advancements in technology and a focus on sustainability will continue to shape the future of quality control in cat litter manufacturing. Embracing these changes and maintaining a commitment to excellence will help manufacturers stay competitive and responsive to the needs of the market.