The Evolution of Geogrid Factories: From Traditional Techniques to Cutting-Edge Innovations
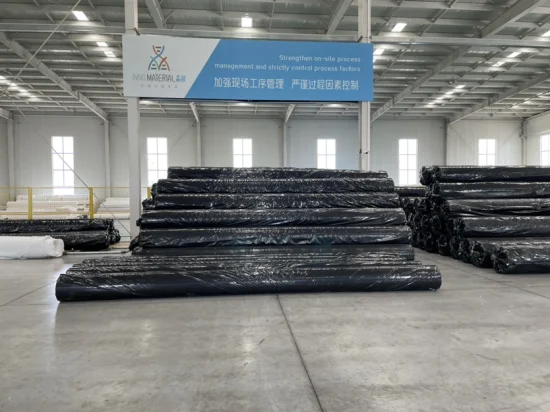
Geogrids have become indispensable in modern construction, offering critical reinforcement and stability for various infrastructure projects. As the construction industry evolves, so too do the technologies and practices within Geogrid factory. This blog explores the evolution of geogrid manufacturing, highlighting the shift from traditional methods to cutting-edge innovations that are shaping the future of reinforcement technology.
The Journey of Geogrid Manufacturing
1. Traditional Geogrid Production Methods
In the early days of geogrid manufacturing, production methods were relatively simple but effective:
Early Extrusion Techniques
- Basic Extrusion Machinery: Initial production relied on basic extrusion equipment to create geogrids, which involved melting polymers and forming them into grid structures.
- Manual Stretching: Manual stretching processes were used to align the polymer chains, though they were less precise compared to modern methods.
Initial Quality Control
- Basic Testing: Quality control in early geogrid production focused on fundamental tests such as tensile strength and material durability.
- Limited Compliance: Compliance with industry standards was basic, with fewer regulations governing performance and safety.
2. The Transition to Modern Manufacturing
As the demand for more advanced geogrid solutions grew, manufacturing techniques began to evolve:
Advancements in Extrusion Technology
- Enhanced Extrusion Machines: Newer extrusion equipment allowed for better control over material thickness and consistency, improving the overall quality of geogrids.
- High-Temperature Processing: Innovations in polymer processing techniques enhanced the strength and durability of geogrids.
Sophisticated Stretching and Forming Techniques
- Uniaxial and Biaxial Stretching: Modern stretching technologies improved the alignment of polymer chains, resulting in higher tensile strength and performance.
- Automated Forming Processes: Automation increased production efficiency and precision, reducing variability and improving product consistency.
Improved Quality Control Practices
- Advanced Testing: Geogrid factories began implementing more comprehensive testing methods to assess various performance metrics, including load distribution and environmental resistance.
- Stringent Compliance: Factories adhered to more stringent industry standards, including ASTM and ISO certifications, ensuring higher levels of safety and reliability.
3. Cutting-Edge Innovations in Geogrid Manufacturing
Recent advancements in geogrid manufacturing have introduced several innovative practices and technologies:
State-of-the-Art Production Technologies
- Precision Extrusion and Stretching: Modern equipment ensures precise material formation and alignment, resulting in geogrids with superior performance characteristics.
- High-Speed Production Lines: Advanced production lines enable faster manufacturing processes without compromising quality.
Innovative Materials and Coatings
- Advanced Polymers: New polymer formulations enhance the mechanical properties of geogrids, making them more effective in various applications.
- Specialized Coatings: Coatings are applied to improve resistance to environmental factors such as UV radiation, chemicals, and moisture.
Sustainable Manufacturing Practices
- Energy-Efficient Technologies: Geogrid factories are adopting energy-efficient machinery and renewable energy sources to reduce their environmental impact.
- Recycling Initiatives: The use of recycled materials in production supports sustainability and reduces waste.
4. The Impact of Geogrid Innovations on Infrastructure
Innovations in geogrid manufacturing are transforming the construction industry, with significant benefits for infrastructure projects:
Enhanced Performance and Durability
- Increased Load-Bearing Capacity: High-strength geogrids provide superior reinforcement, improving the load distribution and stability of infrastructure projects.
- Extended Lifespan: Durable geogrids reduce the need for frequent repairs and maintenance, extending the lifespan of construction projects.
Cost Efficiency and Project Management
- Reduced Construction Costs: Advanced geogrids decrease the need for additional reinforcement, leading to cost savings in construction and maintenance.
- Faster Project Completion: Efficient production processes and high-quality materials enable quicker project timelines.
Environmental Benefits
- Lower Carbon Footprint: Sustainable manufacturing practices and the use of recycled materials contribute to a reduced carbon footprint for geogrid production.
- Greener Construction Practices: High-performance geogrids support environmentally friendly construction methods and contribute to overall sustainability.
5. Future Trends in Geogrid Manufacturing
Looking ahead, several trends are likely to shape the future of geogrid manufacturing:
Integration of Smart Technologies
- Smart Geogrids: Incorporating sensors and monitoring technologies into geogrids could provide real-time data on their performance and structural integrity.
- IoT Integration: The Internet of Things (IoT) may enable better monitoring and management of geogrid applications in construction projects.
Advancements in Material Science
- New Material Developments: Ongoing research in material science will likely lead to the development of geogrids with enhanced properties and functionalities.
- Bio-Based Polymers: The use of bio-based polymers may further reduce the environmental impact of geogrid production.
Global Collaboration and Standards
- International Collaboration: Greater collaboration between manufacturers, researchers, and industry experts will drive innovation and standardization in geogrid technology.
- Harmonized Standards: Efforts to harmonize industry standards globally will ensure consistent quality and performance across different markets.
Conclusion
The evolution of geogrid factories from traditional methods to cutting-edge innovations reflects the ongoing progress in the construction industry. As geogrid manufacturing continues to advance, these innovations are driving improvements in performance, sustainability, and cost-efficiency. By embracing new technologies and practices, geogrid factories are paving the way for more effective reinforcement solutions and contributing to the success of infrastructure projects worldwide. As the industry moves forward, the integration of smart technologies, advancements in material science, and global collaboration will shape the future of geogrid manufacturing and its impact on the construction landscape.