Seasonal Challenges for Cement Contractors and How to Overcome
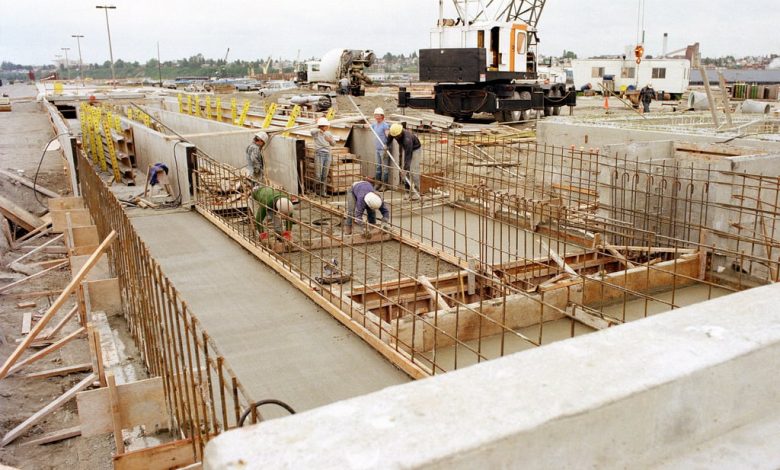
For cement contractors in Savannah, GA, the construction industry is a dynamic field filled with both opportunities and challenges. One of the most significant hurdles these contractors face is dealing with the unpredictable seasonal changes that can have a major impact on their projects. The challenges brought on by extreme weather conditions, varying temperature levels, and other seasonal factors can disrupt timelines, increase costs, and affect the quality of work. The key seasonal challenges faced by cement contractors in Savannah, GA, and explore practical strategies for overcoming them.
Savannah, Georgia, with its humid subtropical climate, is particularly vulnerable to the seasonal extremes that can affect construction projects. Whether you are a part of the best concrete companies in Savannah, GA, or a smaller, independent concrete contractor, understanding how to navigate the changing weather conditions is crucial for maintaining high standards of work and customer satisfaction.
1. The Impact of Humidity and Heat on Concrete
The Challenge: One of the most persistent challenges faced by cement contractors in Savannah, GA, is dealing with the high humidity and heat, especially during the summer months. Savannah’s climate features long, hot summers with average highs often reaching over 90°F, coupled with high humidity levels. These conditions can create difficulties for contractors working with concrete.
High temperatures accelerate the curing process of concrete, leading to a phenomenon known as “hot weather curing.” When concrete cures too quickly, it may not reach its intended strength, leading to cracks, reduced durability, and other structural problems. Additionally, the high humidity can cause moisture retention, which also complicates the curing process.
How to Overcome It: There are several ways cement contractors in Savannah, GA, can mitigate the effects of heat and humidity on concrete projects:
- Use of Retarders: Concrete retarders are chemical additives that slow down the setting time of concrete. By incorporating these products, contractors can prevent the concrete from setting too quickly, ensuring proper curing.
- Cool Down the Concrete Mix: Use cool water to mix the concrete or store materials like sand and aggregates in shaded or air-conditioned spaces to prevent them from absorbing excessive heat.
- Work During Cooler Hours: Scheduling work in the early morning or late afternoon, when temperatures are lower, can significantly reduce the impact of heat on the curing process.
- Moist Curing: Ensure the concrete is kept moist for the first few days after pouring. This can be achieved using curing blankets, wet burlap, or applying a curing compound that helps retain moisture.
For residential concrete contractors in Savannah, GA, these adjustments can prevent costly mistakes that could damage their reputation, as hot weather can be particularly problematic for decorative concrete, such as stamped driveways or patios, which require more precision.
2. Rain and Wet Weather Conditions
The Challenge: Rain is another significant challenge for cement contractors in Savannah, GA. The city is known for its frequent afternoon thunderstorms and rainy seasons, especially during the summer months and hurricane season in late summer and fall. Heavy rainfall can halt construction projects, disrupt schedules, and even damage newly poured concrete.
Wet conditions can also affect the quality of concrete. If rain falls on fresh concrete before it has fully set, it can lead to surface damage, like pitting or washing out the surface, and can ultimately compromise the strength and durability of the structure.
How to Overcome It: Cement contractors in Savannah, GA, need to be proactive when it comes to planning around wet weather:
- Weather Monitoring: Make use of modern technology such as weather apps or websites to track upcoming storms. This will allow contractors to reschedule work in advance, reducing the chances of having to work during wet conditions.
- Temporary Shelters and Tarps: Invest in temporary covers such as tarps, tents, or plastic sheeting to protect freshly poured concrete from rain. Ensuring that the concrete is shielded from rainfall during the curing phase is critical.
- Work Around Weather Windows: In regions like Savannah, GA, where rain is frequent but not constant, it is important for contractors to identify windows of good weather and plan projects accordingly.
- Waterproofing Additives: Adding waterproofing agents to the concrete mix can help make the final product more resistant to water damage, although it won’t prevent damage from rain during the curing stage.
For concrete contractors in Savannah, GA, being able to adapt to sudden changes in weather can save a lot of time and money. Planning ahead and making sure that crews are prepared for rainy conditions is key.
3. Winter Cold and Freezing Conditions
The Challenge: While Savannah’s winters are generally mild compared to many northern states, temperatures can occasionally dip below freezing. Even brief periods of freezing weather can pose a significant threat to concrete work. When the temperature drops too low, the water in the concrete mix can freeze before the concrete has had a chance to cure properly. This can result in delayed setting times, weakened concrete, and surface cracking.
How to Overcome It: Concrete contractors in Savannah, GA, must adopt various strategies to handle the risk of freezing conditions:
- Use Heated Mixes: If temperatures are expected to drop below freezing, it may be necessary to use heated water in the concrete mix or incorporate heated aggregate. This will help maintain the necessary temperature for curing and prevent the concrete from freezing.
- Insulation: Covering freshly poured concrete with insulated blankets or curing blankets will help maintain a consistent temperature, allowing the concrete to continue curing even in cold weather.
- Accelerators in the Mix: Chemical accelerators can speed up the curing process, which is beneficial during cold weather. These additives help reduce the time concrete takes to set and gain strength.
- Avoid Pouring in Freezing Conditions: If the forecast predicts freezing temperatures, it may be best to delay concrete pours until the temperature stabilizes above freezing. For contractors working on outdoor projects like foundations or driveways, delaying the pour can save substantial costs in rework.
For concrete construction companies in Savannah, GA, knowing how to prevent issues caused by low temperatures is vital for maintaining project timelines and quality.
4. Hurricane Season and Storm Surges
The Challenge: Savannah, Georgia, is no stranger to hurricanes and tropical storms. Between June and November, the city is at risk for significant weather events, including strong winds, heavy rains, and storm surges. These can delay construction schedules, cause damage to unfinished work, and even make it dangerous for workers to continue on-site.
How to Overcome It: Here are a few ways contractors can prepare for hurricane season:
- Secure Job Sites: Before hurricane season begins, ensure all job sites are properly secured. This includes removing loose materials and equipment that could become projectiles during high winds.
- Adjust Project Timelines: For larger projects, consider adjusting timelines to accommodate potential storm delays. Knowing that work may be interrupted during hurricane season helps contractors plan buffer periods into their schedules.
- Implement Contingency Plans: Have contingency plans in place for when storms or hurricanes impact projects. This may include moving work to interior spaces, covering ongoing concrete work, or planning for more extensive post-storm clean-up.
- Insurance: Make sure you have proper insurance coverage for storm-related damage. Some best concrete companies in Savannah, GA, may even invest in stormproofing their materials and equipment to reduce the risk of loss.
5. Managing Workforce Availability and Safety
The Challenge: Seasonal weather patterns can affect the availability and productivity of workers. Extreme heat or cold can make working conditions dangerous, and rain or storms can lead to work stoppages. Ensuring worker safety during adverse weather conditions is paramount. Additionally, scheduling issues may arise if workers are unavailable due to seasonal factors like school vacations, holidays, or family commitments.
How to Overcome It: Contractors can improve workforce management by:
- Scheduling Flexibility: Adjust work schedules to account for extreme weather conditions. For example, if it’s too hot or too cold, try to schedule shorter workdays or take frequent breaks to protect workers from heat stroke or frostbite.
- Safety Training: Proper training on weather-related safety measures, such as how to handle extreme temperatures or working in wet conditions, can prevent injuries and ensure projects continue smoothly.
- Maintaining a Pool of Skilled Workers: During peak construction seasons, it may be beneficial to have a larger pool of skilled workers available, as weather-related disruptions may require more labor to meet project deadlines.